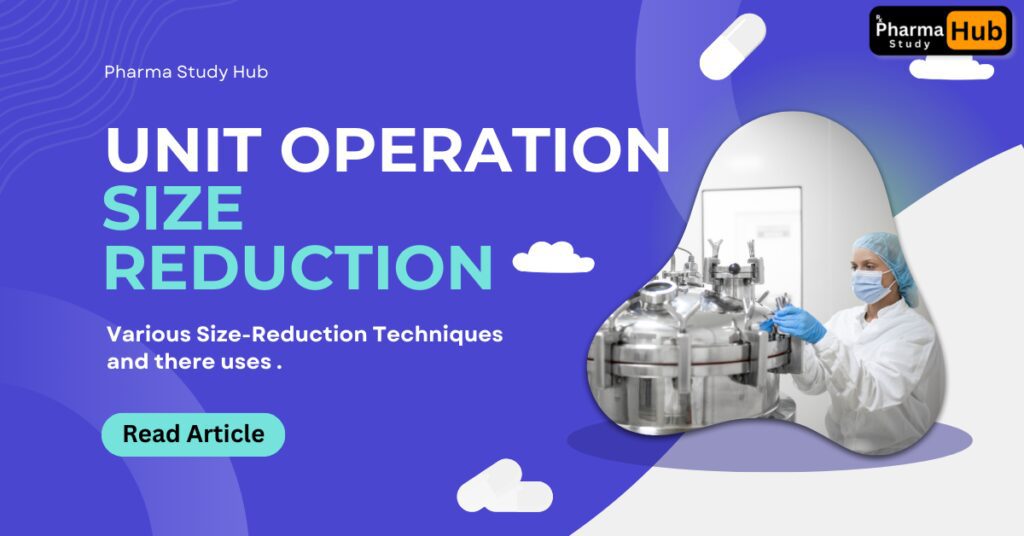
Table of Contents
Introduction - Size Reduction
In the field of pharmacy, the process of size reduction is an essential aspect that influences the development and effectiveness of medicines. Whether it’s tablets, capsules, or ointments, breaking down particles into smaller sizes can make a significant difference in how well a drug works. Size reduction might sound simple, but it’s a critical step in ensuring that medications perform as they should.
In this article, we will discuss the importance of size reduction in pharmacy, its advantages and disadvantages, and the various machines used in the process. Whether you are a student, a pharmacist, or just someone interested in learning more about how medicines are made, this guide will help you understand why size reduction is so important in the pharmaceutical industry.
What is Size Reduction in Pharmacy?
Size reduction in pharmacy refers to the process of breaking down larger particles of solid substances into smaller, more manageable sizes. This process is vital in the pharmaceutical industry because the size of particles can directly influence the effectiveness, absorption, and overall performance of a drug.
To put it simply, when we talk about size reduction, we’re discussing the methods used to reduce the size of raw materials, making them easier to mix, process, and utilize in various pharmaceutical formulations. Whether it’s for creating a smooth cream, a fine powder for tablets, or even ensuring that active ingredients are evenly distributed, size reduction is a key factor.
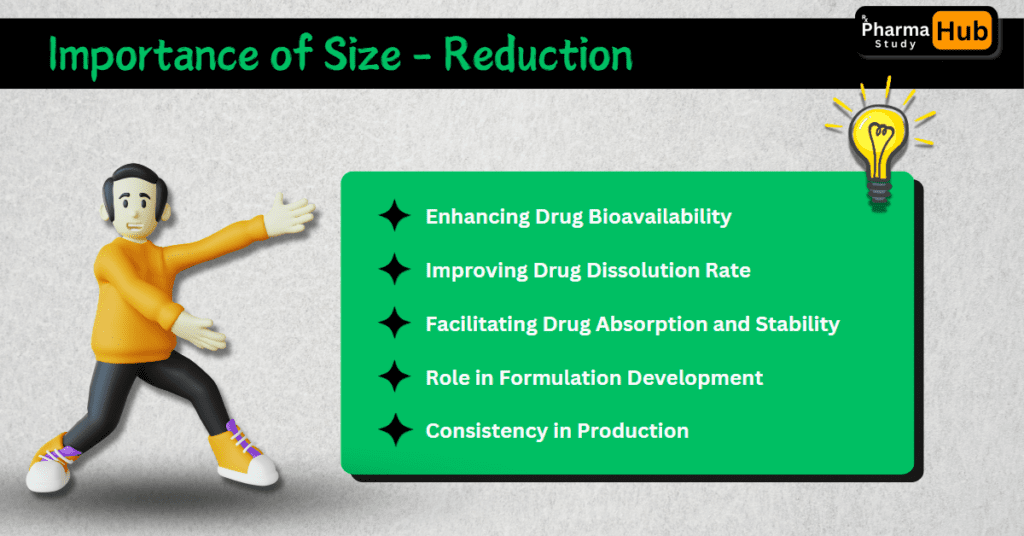
Importance of Size Reduction
- Enhancing Drug Bioavailability: Smaller particles increase the surface area of the drug, which improves its absorption in the body. This means that the medicine can be more effective because it is available for the body to use more efficiently.
- Improving Drug Dissolution Rate: Reducing the size of drug particles helps them dissolve faster. In manufacturing, this ensures that the medicine breaks down quickly once ingested, leading to quicker onset of action.
- Facilitating Drug Absorption and Stability: Smaller particles can be absorbed more easily by the body and can also enhance the stability of the drug. This is important to ensure that the medicine remains effective throughout its shelf life.
- Role in Formulation Development: Size reduction helps in developing various formulations, such as tablets, capsules, and powders. It allows for better control over the release of the drug, making it possible to design medications that meet specific treatment needs.
- Consistency in Production: By standardizing particle size, manufacturers can ensure uniformity in each batch of medicine. This consistency is crucial for maintaining the quality and effectiveness of the final product.
Advantages of Size Reduction
- Increased Surface Area for Better Absorption
- Improved Uniformity in Drug Mixing
- Enhanced Therapeutic Effectiveness
- Simplified Drug Delivery Mechanisms
- It improves the absorption and dissolution rates
- It enhances the drug bioavailability
Disadvantages of Size Reduction
- Potential for Drug Degradation
- Energy Consumption and Cost Implications
- Risk of Contamination and Product Loss
- Challenges in Maintaining Particle Size Consistency
Factors Affecting Size Reduction
- Toughness: The toughness of a material refers to its resistance to breakage. Tough materials require more energy to reduce in size because they resist fragmentation. For example, tough materials like certain polymers or minerals need specialized equipment to achieve the desired particle size.
- Hardness: Hardness indicates how resistant a material is to deformation. Hard materials, such as certain salts or crystals, are more difficult to grind into smaller particles. This often necessitates the use of more robust equipment and higher energy input during size reduction.
- Moisture Content: The moisture content of a material affects its behaviour during size reduction. High moisture content can lead to clumping or stickiness, making it harder to achieve a consistent particle size. Dry materials are generally easier to grind and handle.
- Temperature: Temperature can influence the properties of the material being processed. For instance, increasing temperature can make some materials more pliable, facilitating size reduction. Conversely, very high temperatures might cause certain substances to degrade or change their properties.
- Material Structure: The internal structure of the material, including its crystalline or amorphous nature, impacts how easily it can be broken down. Materials with a crystalline structure might be more brittle and easier to reduce in size compared to amorphous materials, which might be more ductile.
- Feed Size: The size of the material fed into the size reduction equipment affects the efficiency of the process. Larger feed sizes might need pre-crushing or multiple stages of size reduction to achieve the desired final particle size.

Various Techniques of Size Reduction
- Compression: This technique involves applying pressure to reduce the size of particles. In pharmaceutical manufacturing, compression is used to produce tablets by pressing powder into a compact form. It helps in achieving uniform tablet hardness and consistency.
- Cutting: Cutting involves slicing the material into smaller pieces. This technique is commonly used for materials like granules or fibers. Cutting can be done using blades or knives in equipment like mills or granulators.
- Milling: Milling is a process that grinds materials into finer particles using mechanical forces. Different types of mills, such as ball mills, hammer mills, and jet mills, are used depending on the desired particle size and material properties.
- Grinding: Grinding is similar to milling but often refers to processes that produce very fine particles. It involves using abrasive surfaces to reduce particle size. Grinding can be achieved using various grinders, such as edge runners or burr mills.
- Impact: Impact size reduction uses high-speed collisions to break down materials. This can be achieved using equipment like impact mills or hammer mills, where materials are struck by hammers or other hard surfaces to achieve smaller sizes.
- Attrition: Attrition involves rubbing or wearing down materials to reduce their size. This technique is often used in equipment like attrition mills or disc mills, where particles are subjected to frictional forces.
- Shearing: Shearing uses cutting forces to break down materials. This technique is commonly used in equipment like shear mills or granulators, where materials are subjected to shear stress to achieve smaller particle sizes.
- Ultrasonic: Ultrasonic size reduction uses high-frequency sound waves to create cavitation bubbles in a liquid. These bubbles collapse and create high shear forces that break down particles. This technique is often used for materials that are difficult to process by other means.
- Jet Milling: Jet milling uses high-speed air jets to create collisions between particles, leading to size reduction. This method is effective for producing very fine particles and is often used for materials that need to be processed without heat.
- Cryogenic Grinding: Cryogenic grinding involves cooling materials to very low temperatures using liquid nitrogen before grinding. This makes materials brittle and easier to break into smaller sizes, which is useful for materials that are heat-sensitive.
Machines Used in Size Reduction
Classification of Size Reduction Equipment
Crushers:
- Jaw Crushers: These use compressive forces to break down large chunks of material into smaller pieces. They are typically used for coarse size reduction and can handle hard, brittle materials.
- Gyratory Crushers: Similar to jaw crushers, but with a gyrating motion, which provides a more continuous crushing action. They are used for primary crushing in large-scale operations.
- Roll Crushers: These use two counter-rotating rolls to crush material between them. They are suitable for reducing materials to a medium size and are often used in mineral processing.
Grinders:
- Hammer Mills: These use high-speed rotating hammers to impact and break down materials. They are versatile and can handle a range of materials, from coarse to fine, depending on the screen size used.
- Disintegrators: These are similar to hammer mills but have a different rotor design that provides more impact and shear forces. They are used for fine size reduction and can handle tough materials.
- Pin Mills: These use rotating pins or blades to shear and impact the material, leading to fine particle sizes. They are used for materials that require a high degree of size reduction.
Mills:
- Ball Mills: These use rotating cylinders filled with grinding media (balls) to achieve size reduction through impact and attrition. They are commonly used for producing fine powders and can handle both wet and dry materials.
- Attrition Mills: These mills use friction and shear forces to break down materials. They have a rotating disc and stationary plate setup, where materials are ground between the two surfaces.
- Jet Mills: These use high-speed air jets to create collisions between particles, leading to size reduction. They are ideal for producing very fine powders and can operate without heat generation.
Cutters:
- Granulators: These machines cut materials into smaller granules or flakes. They use rotating knives or blades to shear the material, making them suitable for processing large amounts of material into uniform sizes.
- Shredders: These use a combination of cutting and tearing forces to reduce the size of materials. They are used for bulk materials and are often employed in recycling and waste processing.
Pulverizers:
- Roller Pulverizers: These use rollers to crush and grind material into a fine powder. They are commonly used for materials that need to be grind to a very fine size.
- Colloid Mills: These are used to produce fine emulsions or suspensions by grinding materials between a rotating and a stationary surface. They are suitable for applications that require very fine particle sizes.
According to the PCI syllabus we should study in detail about two machine Hammer Mill and Ball Mill, below are the detailed information about these two machines
Ball Mill ⚽
A ball mill is a cylindrical device used in grinding (or mixing) materials like ores, chemicals, ceramic raw materials, and paints. It operates by rotating a cylinder filled with grinding media (balls) which helps in achieving fine particle sizes.
Principle:
The principle of a ball mill is based on the impact and attrition between the grinding balls and the material being ground. As the cylinder rotates, the balls inside are lifted and then fall, causing impacts and grinding action.
Construction:
- Cylinder: A hollow, cylindrical shell that rotates on its horizontal axis. It can be made of various materials such as steel, rubber, or ceramic.
- Grinding Media: Steel balls or other grinding media are placed inside the cylinder. The size and material of the balls affect the grinding efficiency.
- Feed and Discharge Ports: Openings through which material is fed into the mill and where the ground material is discharged.
- Drive Mechanism: Motor and gearbox system that rotates the cylinder at a controlled speed.
Working:
- Loading: Material and grinding media are loaded into the cylinder.
- Rotation: The cylinder is rotated at a specific speed. As it turns, the balls rise along the cylinder’s walls due to centrifugal force.
- Grinding: When the balls reach a certain height, they fall back down, impacting and grinding the material inside.
- Discharge: After grinding, the material is discharged through a port, and the ground product is collected.
Applications:
- Mineral Processing: Grinding ores to liberate valuable minerals.
- Cement Industry: Producing cement by grinding clinker and additives.
- Chemical Industry: Mixing and grinding chemicals for various formulations.
- Pharmaceuticals: Grinding active pharmaceutical ingredients and excipients.
Merits:
- Versatility: Can grind a wide range of materials to fine sizes.
- Uniformity: Produces a consistent particle size and homogeneity.
- Efficiency: Capable of processing large quantities of material.
- Adjustable: Speed and media size can be adjusted to optimize grinding.
Demerits:
- Energy Consumption: High energy requirements for operation.
- Wear and Tear: Grinding media and cylinder lining can wear out over time and require replacement.
- Noise and Vibration: Can generate significant noise and vibrations during operation.
- Over-grinding Risk: There is a risk of over-grinding if not properly controlled, which can lead to excessive fines.
Hammer Mill 🔨
A hammer mill is a type of size reduction machine that uses rapidly moving hammers to impact and break down materials into smaller particles. It is commonly used in various industries for grinding grains, chemicals, and other materials.
Principle:
The principle of a hammer mill is based on impact and shear forces. Hammers, which are mounted on a rotating shaft, strike the material, causing it to shatter into smaller pieces. The size of the output is controlled by adjusting the screen or grate through which the material exits.
Construction:
- Hammer Assembly: Consists of a rotor with swinging hammers or bars attached. These hammers rotate at high speeds to impact the material.
- Casing: The housing encloses the hammer assembly and helps to direct the flow of material.
- Screens or Grates: Positioned around the rotor, these control the size of the particles that pass through. The size of the openings can be adjusted based on the desired particle size.
- Feed Hopper: An inlet where the material is fed into the mill.
- Discharge Port: An outlet where the ground material is expelled from the mill.
Working:
- Feeding: Material is fed into the hammer mill through the feed hopper.
- Impacting: The rotor with hammers rotates at high speed, striking the material and causing it to break into smaller particles.
- Screening: The broken material passes through screens or grates. The size of the particles is determined by the size of the screen openings.
- Discharging: The ground material is expelled through the discharge port.
Applications:
- Agriculture: Grinding grains, such as corn and wheat, for animal feed.
- Food Industry: Milling ingredients for food production.
- Chemical Industry: Grinding chemicals and other materials for formulations.
- Recycling: Shredding and grinding waste materials for recycling purposes.
Merits:
- High Efficiency: Capable of processing large quantities of material quickly.
- Versatility: Suitable for a wide range of materials, including grains, minerals, and chemicals.
- Adjustable Particle Size: Particle size can be controlled by adjusting screen size.
- Cost-Effective: Generally less expensive and requires less maintenance compared to some other size reduction machines.
Demerits:
- Noise and Dust: Hammer mills can generate significant noise and dust during operation.
- Energy Consumption: High energy consumption, especially for large-scale operations.
- Wear and Tear: Hammers and screens can wear out over time and require regular replacement.
- Limited to Coarse Grinding: Not as effective for achieving very fine particle sizes compared to other mills, like ball mills or jet mills.
Conclusion
In pharmacy, size reduction is a crucial process in medication development and manufacturing. By breaking down larger particles into smaller ones, it enhances drug bioavailability, improves dissolution rates, and aids absorption and stability. This process is vital for formulating effective pharmaceutical products. Despite challenges like energy consumption and equipment wear, size reduction ensures the consistency and quality of medications. Whether using ball mills or hammer mills, mastering size reduction techniques is essential for producing reliable and effective medicines.
Let's Connect!
If you enjoyed reading this blog post and found it helpful, I’d really appreciate it if you could share it with others who might benefit from it too. Your support helps me reach more people and continue creating content like this. And if you have any thoughts, suggestions, or ideas, please don’t hesitate to leave a comment below. I’m always eager to hear from you and make improvements based on your feedback. Thank you for being a part of this journey!
1 thought on “Size Reduction in Pharmacy Methods, Machines, and More”